Why Automotive Ethernet Is a Strong Choice
Ethernet has a long and extremely successful history in IT. Invented in 1973 and standardized by the Institute of Electrical and Electronics Engineers (IEEE) in 1985, Ethernet came to dominate local area networks used in business, fending off all competing technologies, such as Token Ring. Ethernet has proven to be a versatile and resilient standard to fuel advances in communications over decades. Versions of Ethernet run over coaxial cable, fiber optics, and unshielded twisted-pair wiring, and speeds have increased from 10M bit/sec to more than 100G bit/sec. Ethernet is well understood and refined after decades of use.
As automotive networks began to connect more computing resources in vehicles, it was only natural to turn to Ethernet, and in 2016 the IEEE published the first Automotive Ethernet standard, IEEE 802.3bw or 100Base-T1. While the bandwidth of 100M bit/sec is comparable to the 100Base-TX introduced in 1995, there are key differences in the automotive version.
Both standards run on unshielded twisted-pair wiring, where two copper wires are twisted together along the length of the cable. This has the effect of producing less electromagnetic radiation and cross-talk that could interfere with other wires or components, while also resisting interference from other sources.
However, 100Base-TX uses two wire pairs, while Automotive Ethernet uses a single pair, immediately reducing weight and cost. The pair is “balanced,” meaning the signals have equal but opposite voltages. Transmit and receive signals are both conducted on the single pair, instead of on the separate pairs of 100Base-TX.
The 100Base-TX standard was also specified for a maximum length of 100 meters, a length that subsequent Ethernet standards have adhered to. Automotive Ethernet was specified for a maximum of just 15 meters. Obviously, automotive applications don’t need the longer distance to network components within a vehicle, and the shorter length allows for lighter cabling.
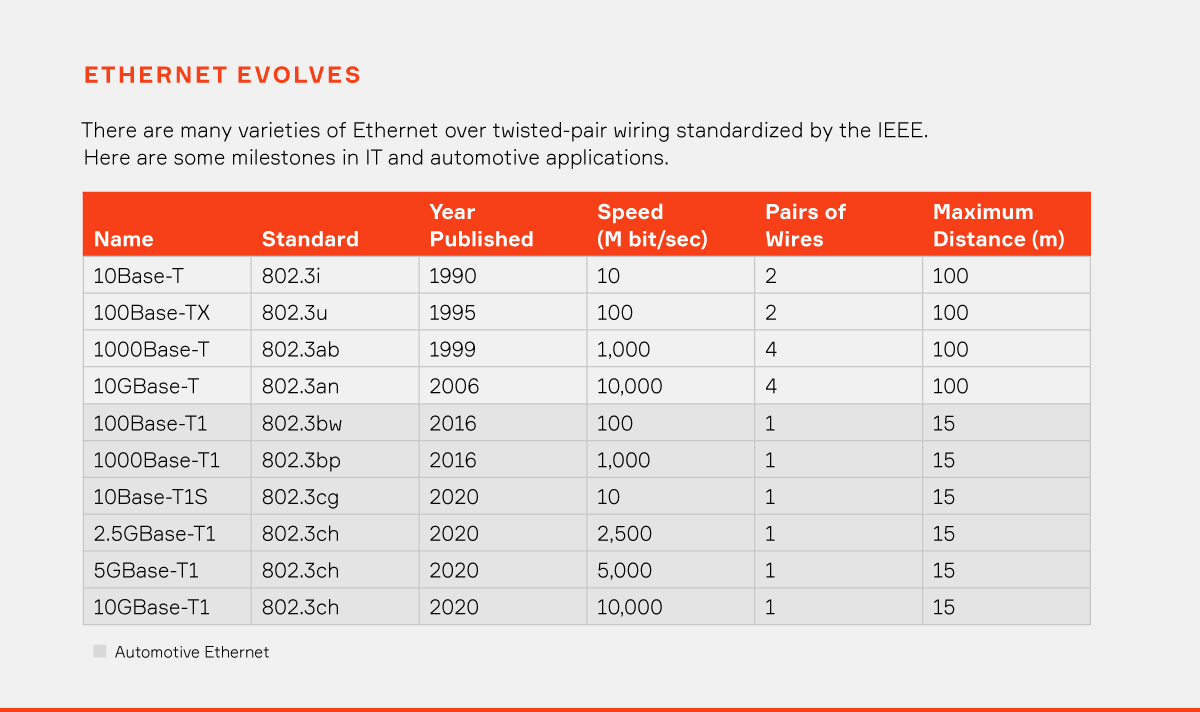
Next steps in Automotive Ethernet
The 100M bit/sec of the IEEE 802.3bw standard can cover many initial automotive applications, so it is widely used today. But as we look ahead to higher-definition video streams and aggregation of data from multiple sensors onto common cables, higher speeds will be necessary.
Soon after IEEE 802.3bw was finalized, the IEEE ratified 802.3bp, or 1000Base-T1, allowing for gigabit speeds over shielded or unshielded twisted-pair wiring. This standard shares many attributes with its predecessor, but the frequency is nearly 10 times as high, at 600 MHz. This means that the cables are more vulnerable to cross-talk, and engineers have to keep this in mind when they design systems, as they manage electromagnetic noise throughout the vehicle, testing rigorously and shielding where needed. This standard will provide enough bandwidth for the next two or three platform generations.
In 2020, the IEEE produced 802.3ch, which provides for multigigabit Ethernet at standard rates of 2.5G bit/sec, 5G bit/sec and 10G bit/sec over the same 15 meters. Shielded twisted pair wires will operate at these speeds, but electrical frequencies in excess of 7 GHz may require the use of shielded parallel pair wires to minimize EMI issues.
A key benefit of Ethernet is that it is a flexible network, allowing easy reconfigurations. If there is a failure, an Ethernet router can route data traffic a different way. This is important to ensure uninterrupted connectivity for major compute components in a vehicle.
Also critical in vehicle networks is copper-based Ethernet’s ability to carry electrical power along with the data signal, a feature called Power over Data Lines (PoDL). PoDL can support up to 500 mA of power, enough for certain sensors, such as an optimized satellite camera. This allows vehicle manufacturers to run a single pair of wires to some sensors for all of their needs, reducing weight and simplifying the architecture.
Aptiv’s position as the provider of both the brain and the nervous system for vehicles gives us a unique perspective on the important role of data connectivity, a perspective we have leveraged to inform our Smart Vehicle Architecture™ approach to next-generation electrical/electronic architecture. SVA™ requires that solutions provide a robust foundation for all of the components that make active safety possible, while at the same time reducing vehicle weight and enabling innovation to thrive. Automotive Ethernet presents one of the most promising opportunities to build vehicles that meet those standards.
Learn more about the data connectivity standards that will drive innovation in automotive in our white paper.